What is Warehouse Robotics? The Ultimate Guide for 2022
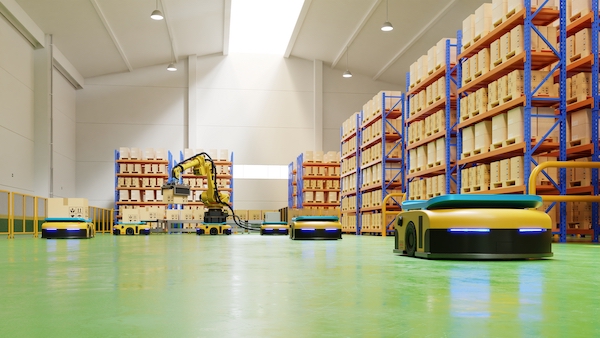
What is Warehouse Robotics? The Ultimate Guide for 2022
Manual warehouse work is ideally suited for automation and, more specifically, robotics as a form of automation. It fulfills at least two out of the three “Ds” of robotization: dirty, dangerous, and dull. Warehouses might not be dirty — at least not in an ideal world — but the job can be dangerous, and it’s certainly repetitive.
Industry experts have eyed warehouse jobs as candidates for automation practically since the invention of robots themselves, but the field has only recently expanded to a suitable state. Warehouse robots are usually mobile, very heavy, and can lift thousands of pounds. New technology makes it possible for these machines to share space with human workers safely.
It may take years before there’s ever such a thing as a fully robotic warehouse — robots are still too bulky for many jobs, and they can be too expensive to scale. However, when humans and machines work in concert, the result is ultimately a safer and more efficient workplace.
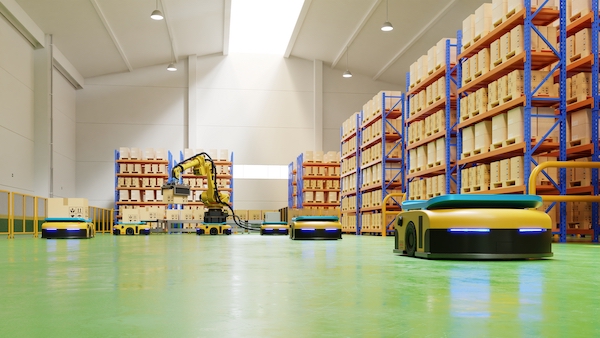
What Is Warehouse Robotics?
A warehouse robot is an autonomous machine designed to replace or augment human effort in a factory environment as a form of automation. Robots in this context are a two-part system — there’s the machine itself, which is specialized for a single task, and there’s the software that controls it. Robots are usually single-purpose machines. Some are solely designed to transfer material between warehouse slots or between slots and the loading dock. Other robots can reconfigure the warehouse itself, moving entire racks around to create a more efficient space.
In recent years, robotics companies have made significant strides with warehouse robots. While previous models were little more than automated trams running on rails, the latest versions have advanced features, like sensors, that determine if there’s an obstacle in their path and allow the robot to safely move around it. They can alter their routes based on available stock. Some robots are even advanced enough to handle delicate items or unload shipping containers.
Key Takeaways
- Warehouse robotics technology is rapidly advancing, making it a fit for a growing number of businesses in different industries.
- New sensor technology means that robots can navigate the warehouse autonomously.
- In addition to bulk transport of goods, robots can pick, pack and palletize items, dramatically simplifying the fulfillment process.
- “Cobots” now work alongside human personnel, augmenting their abilities and preventing fatigue and burnout.
Warehouse Robotics Explained
Aside from technological advancements, one of the big reasons why warehouse automation has risen in prominence is because warehouse work takes a toll on human workers. Warehouse work involves lifting, stretching bending, and walking, sometimes while carrying heavy objects. This work is a significant amount of strain over an eight-hour shift, and it can be easy for warehouse workers to injure themselves via repetitive strain or accidents.
On the other hand, robots do not get tired — and if they do, all they need to do is recharge next to a power outlet. If their joints get strained, they can be replaced. Bending, stretching, and carrying heavy objects don’t pose physical risks. Ideally, you’ll be able to move workers from stressful and potentially injurious jobs — like unloading shipping containers — to positions like picking and packing where their skills can still outstrip robotic counterparts.
Why Is Warehouse Robotics So Popular?
The rising popularity of e-commerce over the last few decades has also fueled demand for warehouse robotics. Not only are customers ordering more products online, they’re also demanding faster shipping. And at the same time, warehouses and fulfillment centers have not seen budget increases to account for this increased volume. These realities mean warehouses must get their products from slots to the loading dock faster than ever.
Warehouse robotics use software and hardware to improve operations, making fulfillment faster and less demanding. For example, the warehouse management system (WMS) might notice a spike in orders for three products. The WMS could then direct its connected robots to re-slot these items closer to the loading dock in a way that doesn’t upset existing operations. When it’s time to fulfill these orders, human workers can pick orders or build pallets faster because they don’t need to walk as far.
Types of Warehouse Robotics
Recent advancements in the warehousing industry mean there are now several kinds of robots specializing in different tasks. These can range from checking inventory levels to physically moving goods from place to place.
- Automated Guided Vehicles (AGV):Forklifts or pick carts require human drivers, but AGVs can replace them, navigating the warehouse using embedded markers or advanced LiDAR, a technology which uses robots to receive the world by recording reflections from a spinning laser array.
- Autonomous Mobile Robots (AMR):While an AGV can either use tracks or sensors to navigate the warehouse, the AMR only uses sensors such as LiDAR, infrared or onboard cameras to get around. Because these robots can create their own routes, they can generate major efficiency gains. In addition, they can route intelligently around obstacles instead of stopping in their tracks.
- Aerial Drones:Flying drones can move at high speeds, and they’re small enough to get places where workers can’t. This feature makes them ideal for tasks such as inventory scanning — they can fly to a slot, estimate the amount of material inside and automatically update the inventory management system.
- Unmanned Aerial Vehicles (UAV):UAVs can perform the same tasks as aerial drones, but these robots are controlled by human operators instead of autonomous navigation.
- Automated Guided Carts (AGC):This type of robot is essentially the same as an AGV, but an AGC is designed to carry smaller amounts of material.
- Automated Storage & Retrieval Systems (AS/RS):AS/RS robots are designed with mobility in mind. While moving on fixed tracks, these robots use cranes or lifters to move through warehouse aisles and retrieve products from wherever they sit. These are most often used alongside a WMS.
- Collaborative Robots (Cobots):Cobots split the difference between complete autonomy and human control. Many of them are programmed to follow human workers around as they pick various orders. Others are simply designed to work autonomously in areas where humans are also working — because of their advanced sensors, there’s little risk of collision.
- Articulated Robotic Arms:As the description suggests, these robots are just arms and are sometimes attached to a wheeled base for transport. These can be used to pick items, pack them, assemble components, unload containers or construct pallets.
- Goods-to-Person (G2P):With goods-to-person, warehouses can do away with sending out employees to pull items from shelves. Instead, pickers stay in the same place and the G2P vehicle delivers items to them.
Benefits of Warehouse Robotics
From increased worker safety to improved inventory management, many companies have reaped the benefits of warehouse robotics. In fact, warehouses with a robotics infrastructure often have a competitive advantage over those that haven’t adopted this technology. Key benefits of warehouse robotics include:
- Improved worker safety.Robots help lift heavy objects and minimize the need for workers to travel long distances on foot. This feature helps decrease the risk of repetitive stress injuries on the job.
- Increased productivity.Warehouse robots can help workers move inventory into a centralized area for picking, making it easier and faster to assemble pallets or individual orders.
- Optimized storage.Some robots can store and retrieve inventory (often by physically moving warehouse shelves) from areas where human workers can’t reach. This benefit means warehouses can pack shelves closer together, increasing storage space.
- Automated replenishment.Robots can handle the often-repetitive work involved with moving inventory from buffer stock areas to warehouse slots, allowing workers to spend more time picking and packing orders.
- Recruiting.When you acquire and use robots in your warehouse, your business might become a more appealing place to work and attract a better pool of candidates.
What Industries Use Warehouse Robots?
Nearly every industry can use warehouse robotics, but adoption is growing faster in certain sectors. Online retail, as mentioned earlier, is implementing robotics at a rapid rate. As of 2019, Amazon, for example, operated over 200,000 robots in its warehouses, and other e-commerce giants have been quick to follow suit. Walmart, for example, is adding autonomous robots to 25 of its distribution centers starting in 2021, according to TechCrunch.
Other sectors embracing robotics include the food and beverage industry, which relies on speedy and accurate handling to get perishable items into consumers’ hands quickly. The automotive industry was one of the first to leverage robotics, employing it on assembly lines, and now those companies are swiftly automating other aspects of their operations. Lastly, pharmaceutical companies require extreme precision in their supply chain, with the need to track the source and history of every pill they produce, and they increasingly rely on robots to help them meet these standards.
Warehouse Robotics Use Cases
We’ve spoken generally about the tasks robots can accomplish in the warehouse. Now, let’s narrow it down. It’s important to know that robots are specialists — a robot designed for picking probably won’t be great at transportation or delivery. What tasks can robots accomplish?
- Picking:Warehouse robots can travel through the warehouse faster than human workers and choose more efficient routes, allowing them to fulfill orders faster.
- Sorting:Robots use computer vision systems combined with conveyor belts and mechanized arms to identify products and route them to the proper bins and warehouse slots. This task is one of the most complex that a robot can perform.
- Loading and Unloading:Newer robots, such as Stretch from Boston Dynamics, are designed to physically load or unload trucks using arms and computer vision systems.
- Palletizing and Depalletizing:Similarly, robots can use these same systems to load pallets or break them down. Thanks to artificial intelligence, robots can build pallets for maximum stability and protection depending on the products being loaded.
- Packaging:Some robots can use specialized limbs and grippers to place items inside of boxes or bags. They can also automatically calculate the size of the box needed to accommodate a particular item.
- Transportation:Some robots are designed to replace forklifts by automatically moving bins or pallets from one end of the warehouse to the other.
- Delivery:A few advanced robots take the form of autonomous vehicles (usually smaller than passenger cars) to make deliveries from the warehouse to the consumer. Several grocery and ecommerce companies have piloted this approach, though it’s only available in a few cities for now.
- Replenishment:Robots, such as UAVs, can sense when stocking levels are too low, prompting AGVs to automatically replenish the appropriate bins.
How Do Warehouse Robots Navigate Warehouses?
Safety is paramount in the warehouse. With multi-ton autonomous robots wandering around, it’s essential to ensure these vehicles have a safe way to avoid workers and other equipment.
- Rail Navigation:Rails are the simplest way for a robot to navigate a facility. By following a rail mounted to the floor, the robot cannot deviate from its track and cause other problems.
- Wire-Guided Navigation:Robots use sensors to detect the electromagnetic current of a wire mounted underneath the floor. The robot still can’t deviate from its course, but removing the rail avoids a trip hazard for workers.
- Magnetic Tape-Based Navigation:Similar to wire-guided navigation, robots follow the magnetic field created by magnetic tape. Since the tape is easier to install than wires or rails, it’s easier to reroute robots when necessary.
- Label-Based Navigation:Under this method, robots navigate by following a series of labels resembling QR codes. These help robots classify where they are and what they’re looking at, understanding them as doors, racks, pallets, bins and more.
- Laser-Based Navigation:Lasers are an essential component of label-based navigation, but lasers can also be used independently. A worker with a laser scanner can walk around the warehouse to create a 3D map that a robot can later use to guide itself.
- Vision-Based Navigation:Vision-based navigation systems are a category encompassing lasers but also include photometric cameras. In other words, some robots can use a digital camera combined with image recognition to guide themselves around an environment.
- Geo-Guidance:In some cases, robots can orient themselves by using landmarks within the loading environment, such as the loading dock or specifically marked racks and walls. These landmarks help guide robots equipped with geo-guidance.
- LiDAR (Light Detection and Ranging):LiDAR is the latest technology in autonomous robots — a sensor emitting lasers hundreds of times per second in all directions to create a “point cloud” that resolves itself into a complete map of the warehouse (plus moving obstacles such as workers and other robots.)
History of Warehouse Robotics
The history of robots in the warehouse is relatively short. In 1961, General Motors became the first company to install a warehouse robot — a robotic arm known as Unimate, which was used to remove parts from die-casting machines.
Preprogrammed arms and vehicles running on rails or wires represented “state-of-the-art” warehouse robotics until the turn of the 21st century. Three things happened around that time: First, powerful computing hardware became more affordable. Next, robotics designers began using this hardware in combination with advanced sensors. This allowed robots to conduct image recognition in real-time, the first step towards autonomy. Lastly, military organizations such as DARPA became interested in the concept of autonomy and began sponsoring challenges for organizations that could create autonomous vehicles and robots.
These advancements eventually trickled from the lab to the industrial sector, resulting in the creation of robots that could navigate the warehouse without endangering humans or the building itself.
Warehouse Robotics Trends
Over the past few years, robotics use has exploded due to technological breakthroughs, the increasing popularity of online shopping, and rising customer expectations for fast delivery. As a result, many novel kinds of robotic systems have gained traction.
For example, most warehouse robots perform only one function, but companies are now experimenting with multipurpose robots. Instead of buying various robots for multiple jobs, businesses can now purchase one robot for multiple operations like picking, loading, packing, and unpacking, for example.
Lastly, companies want to ensure that they can augment their human workforce and prevent the turnover of trained staff due to burnout. G2P robots and cobots are the latest examples of this trend. G2P robots are designed to prevent workers from walking miles across the warehouse every day, while cobots follow human workers and help them do their jobs. For instance, the human might hand items to a robot, which then packs and palletizes them.
Fast-Track Efficiency With Warehouse Robotics and Software
Warehouse robotics may seem like an expensive investment, but they’re able to perform a number of different tasks in this environment without ever getting tired or injured. Using these systems helps companies eliminate repetitive and dangerous tasks while increasing their efficiency, productivity, and revenue, providing a significant competitive advantage.
When robots are paired with leading supply chain management solutions, businesses can automate more processes and unlock new efficiencies across their warehouse. By using robots, a company might be able to replenish its inventory without manually checking stock levels. It can increase warehouse productivity by moving products to where workers are instead of the other way around. Once your operation reaches a certain size and you have the right systems in place, robotics often justify the upfront investment.
Warehouse robotics has come a long way. In the beginning, warehouse robots were bolted to the floor, able to perform only the simplest preplanned motions. As time went on, warehouse robots gained first movement, then autonomy. Although robots might never truly control a warehouse, warehouse management software and robotics now work together to augment human effort and planning capabilities, resulting in a warehouse that’s safer, faster, and more efficient.
By Abby Jenkins
The post What is Warehouse Robotics? The Ultimate Guide for 2022 appeared first on ERP News.